Rethinking Position Sensing in the Age of the Electric Vehicle
- Marketing Artimar
- 14 abr 2023
- 3 Min. de lectura
Increasing numbers of stray magnetic fields impact the operation and reliability of magnet-based sensors.

Hall Effect Sensors in Electric Vehicles (EVs)
With applications ranging from determining the position of the steering wheel, pedals and seats to the settings of various valves, knobs and actuators, position sensors are a common feature in modern automobiles. Traditionally, Hall effect sensors were used for this purpose because of the many advantages that they provide, including high reliability (because they function without physical contact) and high-speed operation. However, the EV is a vastly different environment than that of the traditional internal combustion engine-powered vehicle that it is gradually replacing, and this creates problems for the continued use of Hall effect sensors. In this post we review the operation of the Hall effect sensor and explain why it is unsuitable for use in EVs. We will then show how inductive position sensors operate and what makes them a better alternative for position sensing applications in EVs.
Problem Using Hall Effect Sensors in EVs
Hall effect position sensors generate a small voltage in response to the magnetic field strength from a permanent magnet target. The output voltage can be used to measure the distance between the magnet and the Hall effect Integrated Circuit (IC). However, a problem occurs if something else introduces a magnetic field in the same vicinity as the Hall effect IC. If this happens, then the sensor output voltage is not reliable. To prevent this happening in automobile applications, shielding is often used to protect the sensor from the effect of stray magnetic fields in a vehicle. While this approach has been satisfactory in conventional vehicles, EVs present a much tougher challenge for Hall effect sensors. In an EV, low-frequency magnetic fields are generated by the four primary high-voltage modules—namely the powertrain module, the On-Board Charger (OBC), the battery pack and the DC-DC module—and these can affect some Electronic Control Units (ECUs) in a vehicle. The brushless DC motors used for power steering and brake assist also contribute to this problem.

Figure 1: Magnetic Fields Within an EV
An ECU with Hall effect sensors that is situated near the battery pack or powertrain modules could be affected by the low-frequency magnetic field if there is insufficient shielding provided. The requirement for extra shielding in EVs means bigger and heavier sensors—both of which are undesirable when trying to extend the battery life and hence the range of a vehicle. Due to the rapid increase in the number of stray magnetic fields, new automobile specifications require even more immunity tests at higher magnetic fields. Car electronics are now subjected to over a 5 mT (millitesla) DC field and frequencies up to 150 kHz AC fields during Electromagnetic Compatibility (EMC) qualification. False readings in any of the safety-critical sensors—power steering, accelerator pedal, traction rotor position—are intolerable.
Inductive Sensor Advantage
Inductive proximity sensors like our LX3302A work by inducing a current in a metal object which is within the operating range of the sensor. The sensor generates a magnetic field using an oscillator. Two secondary coils are used to detect this magnetic field, and just like when using a transformer, Faraday’s law converts this field into a voltage. A metal target that interferes with this magnetic field will induce eddy currents that oppose its effect and reduce the field strength to zero at the target. Two receiving coils placed in different physical locations detect different voltages, the ratio of which can then be used to determine the position of the target object.
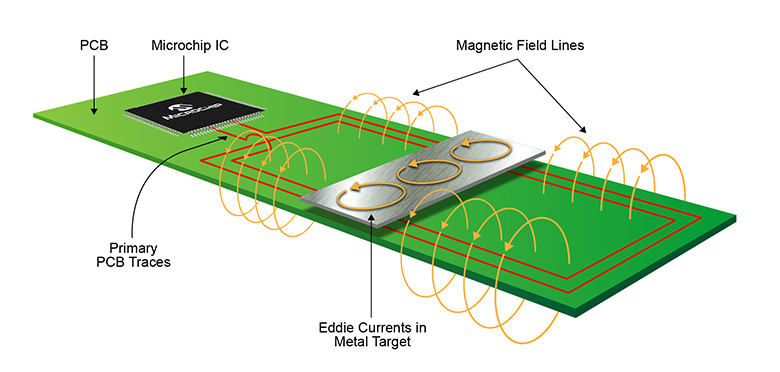
Stray magnetic fields are not a problem for inductive sensors which use a technique called active demodulation. This filters out any unwanted external fields so that the sensor only detects the signal frequency of interest. Also, because inductive position sensors use Faraday’s law, which reacts only to AC fields, they don’t pick up any external DC magnetic fields. Other advantages of using inductive sensors include:
Inductive sensors have better performance at higher temperatures than magnet-based sensors and in high temperature environments, the signal processing electronics are not required to be near the sensing coils. Magnetic sensors require electronic conditioning circuitry to be located at the sensing point. Inductive position sensors are very accurate and can be used to measure linear positions up to many different lengths (5–600 mm). They are also easier to install because they only require a metal target and can be built directly into an ECU. Hall sensors require a magnet which must be incorporated into its installation.
To learn more inductive position sensors and how to use our LX3301A and the LX3302A inductive sensor interface ICs in your application, visit our inductive position sensor web page.
Mark Smith, Nov 15, 2022
Tags/Keywords: Automotive and Transportation
Comments